浅谈晶圆检测技术——光学检测是最合适的道路吗?


半导体芯片,这个在现代科技领域中早已家喻户晓的名词,无疑是当今科技迅猛发展的象征之一。它如同一位幕后英雄,默默地推动着智能手机、电脑、汽车、航空航天等众多行业的进步,使我们的生活变得更加丰富多彩和高效便捷。而晶圆作为半导体产业的核心基石,其重要性不言而喻。
晶圆的品质直接关系到芯片的性能和可靠性,可以说,晶圆的优劣在很大程度上决定了芯片能否在激烈的市场竞争中脱颖而出,是成为一颗璀璨的明星,还是黯然失色。在晶圆的生产过程中,每一道工序都如同一场紧张刺激的角逐,各种先进的检测技术则如同严苛的评委,对晶圆进行全方位、无死角的审视和评估,确保其达到高标准的要求。
其中,光学检测技术因其高效、无损等优点备受业界关注,成为众多检测方法中的热门选手。然而,光学检测是否真的是那条完美无缺、无可替代的“冠军之路”呢?实际上,每种检测技术都有其独特的适用范围和局限性,光学检测虽然在某些方面表现出色,但在面对一些特殊的检测需求时,可能仍需与其他技术相结合,才能发挥出最佳的效果。因此,在晶圆检测领域,多种检测技术的协同合作才是实现全面质量控制的关键所在。
在探究光学检测技术之前,让我们先来看看较为传统的那些检测方法都是什么原理,它们在半导体缺陷的检测过程中都有哪些优势与劣势:
化学腐蚀检测
化学腐蚀检测是过去行业内运用较为广泛的检测方法之一,其运用化学试剂对晶圆表面进行选择性腐蚀,之后通过观察腐蚀后的表面形貌来发现潜在缺陷。在半导体材料中,如位错、空位等缺陷都会导致局部晶格畸变,使得这些区域的表面能增加。当化学腐蚀剂与材料接触时,缺陷区域由于表面能较高,会优先发生腐蚀反应,形成腐蚀坑。通过观察这些腐蚀坑的形状、大小和分布,可以推断出缺陷的类型和密度。常用的腐蚀剂包括酸性溶液和碱性溶液。例如,硅材料常用的腐蚀剂有氢氟酸(HF)和硝酸(HNO3)的混合溶液,而碳化硅则常用氢氧化钾(KOH)。腐蚀剂的选择和配比会影响腐蚀速度和腐蚀坑的形态。该检测技术能够检测到微小的缺陷,如纳米级别的位错,相对于其他检测方法,化学腐蚀检测设备简单,成本较低。然而,化学腐蚀检测过程中可能会对样品表面造成一定的损伤,影响样品的后续使用和性能,对于一些结构较为脆弱的半导体材料,过度腐蚀可能导致材料结构的破坏。除此之外,常用的腐蚀剂如氢氟酸、氢氧化钾等具有较强的腐蚀性和毒性,使用过程中容易对环境造成污染。
电学检测
电学检测也是晶圆检测领域不可忽视的一员。其基本原理是通过测量晶圆的电学参数,如电阻率、电容、电感等,来确保其符合设计要求和质量标准。该技术广泛应用于晶圆测试和芯片测试,分别在晶圆加工完成后和晶圆切割成芯片后进行,以识别正常工作的芯片并确保其性能符合要求。此外,电学检测还用于工艺监控,以确保生产过程的稳定性和一致性。其特点包括高精度、多功能性和实时监控能力,能够精确测量多种电学参数,并在生产线上实时进行检测。常用的设备包括探针台和测试机,结合自动化系统,提高了检测的效率和准确性.不过,电学检测对于设备的校准要求极高,微小的误差都可能导致误判,而且检测过程相对复杂,耗时较长。
原子力显微镜(AFM)检测
原子力显微镜(AFM)是一种利用微悬臂和探针与样品表面相互作用力来获取样品表面形貌信息的技术。其原理是通过探针扫描样品表面,探针与样品之间的相互作用力导致悬臂发生偏转,这种偏转被检测系统转换为电信号,并通过反馈系统调节探针与样品的距离,从而获得样品的表面形貌图像。AFM的优势在于其高空间分辨率,能够在纳米级别上量化表面粗糙度,并且适用于导电和绝缘样品。此外,AFM可以在大气和液体环境下工作,无需对样品进行特殊处理,是一种无损检测技术。然而,AFM也存在一些不足之处,如成像速度较慢,尤其在大范围样品的检测中效率较低。此外,AFM的操作较为复杂,需要专业的技术训练,并且对样品的力学性质有一定的依赖性,软样品可能因探针压力而变形。
(AFM检测中探针运作示意图)
X射线检测
半导体晶圆的X射线检测技术基于X射线的高渗透性,通过X射线穿透晶圆并利用不同材料对X射线的吸收和衍射差异来生成影像,从而揭示晶圆内部的结构和缺陷。这种技术具有无损检测的优点,不需要对样品进行切割或破坏,因此不会对晶圆造成损害。同时,X射线检测具有高分辨率,能够清晰地显示微米甚至纳米级别的缺陷,这对于现代半导体制造中对精度要求极高的检测尤为重要。此外,X射线检测能够提供深度信息,使得对封装内部或芯片内部的缺陷检测成为可能。然而,X射线检测也存在一些不足之处,例如设备成本较高,且设备通常体积较大,这可能限制了其在某些环境下的应用。此外,X射线检测过程中会产生辐射,需要采取适当的防护措施以保护工作人员和环境。
(X射线检测系统示意图)
电子束检测
电子束检测是利用高能电子束与晶圆表面相互作用,激发出二次电子,通过收集和分析这些二次电子来检测晶圆的缺陷和关键尺寸。其优点在于灵敏度高,能够检测到非常小的缺陷,如栅极刻蚀残留物等,且不受某些表面物理性质的影响。此外,电子束检测可以在线检测,具有即时性和预判性,能够在制程早期发现缺陷。然而,该技术也存在一些不足之处,如检测速度较慢,成本较高,且在大面积晶圆扫描时效率较低。这些因素限制了其在大规模生产中的应用,通常需要与其他检测技术如光学检测结合使用,以提高检测效率和准确性。
(电子束检测原理示意图)
光学无损检测
光学检测是利用高分辨率的光学显微镜来观察晶圆表面以识别缺陷,主要包括明场照明和暗场照明两种方式。明场检测是通过检测反射光的强度变化来识别缺陷。适用于检测较大的缺陷,如划痕、颗粒等;而暗场检测则主要检测散射光,适用于检测较小的缺陷,如亚100纳米级别的缺陷。除此之外,部分高端检测设备也同时配备了光致发光检测通道。光致发光检测的基本原理是利用光激发材料的电子从价带跃迁到导带,形成电子-空穴对。这些电子和空穴在复合过程中释放出光子,形成光致发光。通过测量这些光子的光谱特性,可以获得材料的电子结构、缺陷态密度、能级结构等信息。
目前,清软微视(杭州)科技有限公司研发生产的Omega 9880无图形晶圆缺陷检测设备的光路系统正是高度集成了明场(含DIC)、暗场和光致发光等成像方式,能够清晰地成像化合物半导体衬底和外延的缺陷。光致发光通道的高效率激发和多通道采集技术使得晶格缺陷的成像更加清晰,细节更加丰富。此外,Omega 9880还具备白点检测、Hazemap输出、自定义检测规则等功能,支持衬底、外延、芯片全制程段的缺陷叠图,提供全面的缺陷失效分析能力。其先进的软件功能和人工智能图像处理算法能够迅速且精准地识别与分类各类缺陷,为生产决策提供可靠的数据支持。
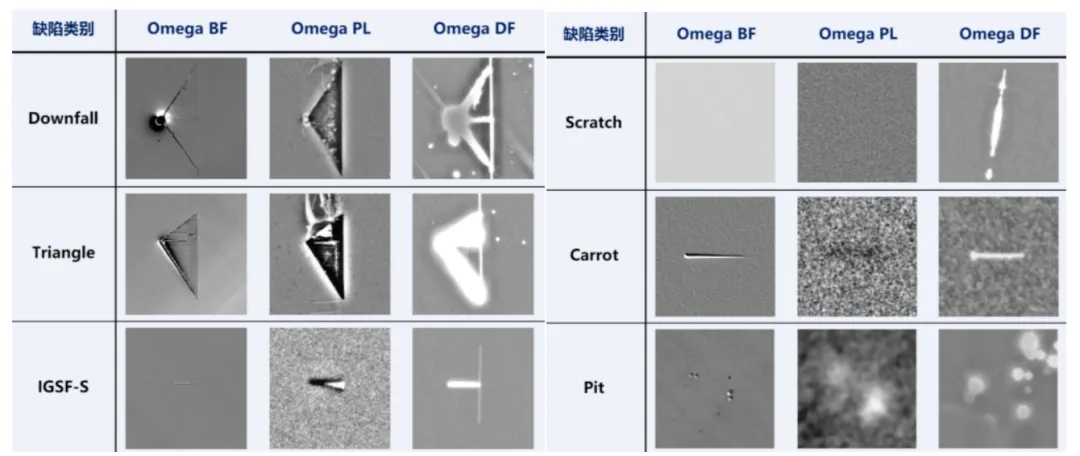
未来,光学检测技术将通过提高光学分辨率,并结合图像信号处理算法,进一步提高检测精度。随着激光技术的突破和晶圆光刻光源EUV的降维下放测量,光学量测设备有望在更先进的制程节点发挥作用。同时,智能化自动化程度也会不断提高,借助人工智能和机器学习算法,实现缺陷的自动识别、分类和分析,减少人工干预,提高检测效率和准确性。
然而,要说光学AOI是最有效的检测技术也不尽然。虽然它在速度、成本和大规模生产方面具有显著优势,但在检测一些纳米级别的微小缺陷时,其精度相对电子束检测等技术可能略显不足。而且,对于晶圆内部的缺陷,光学AOI也无法像X射线检测那样直接进行检测。在实际应用中,通常需要根据具体的检测需求和场景,将光学AOI与其他检测技术相结合,发挥各自的优势,才能实现更全面、更准确的晶圆检测。随着半导体工艺的不断进步,检测技术将不断创新升级,向更高精度、更高速度、更高智能化方向发展,同时国产替代进程也将加速推进,为我国半导体产业的发展提供有力支持。